概述
怎样设定及持续监测炉温是PCB组装行业最主要的难题,为了达到高质量的焊接,需要控制与回流炉相关的一切因素,并了解回流炉是怎样工作的。
什么是温度曲线
通常的回流炉中,PCB会从炉子的一端进入炉膛,以相同速度通过加热区(见图1)。温度曲线就是事实描绘出PCB在通过炉膛时的温度变化,曲线与温度、时间及加热效率有关。
通过粘贴在PCB的热电偶可以测量出各个点的温度,热电偶被事先固定在测试点上, 一般使用线径为30-36 g的线,用高温胶带、胶水或者高温锡线固定。.用高温胶带粘贴比较简单,但是温度是不准确的。 可以使用熔点为286度的10-88-2的锡合金来焊接热电偶。
描绘PCB的曲线图
图2展示了PCB上三根热电偶的曲线,其中TC2在TC1后面5’’,TC3在TC2后面3’’。
用温度VS距离来记录曲线可以很直观的看出 (见图 3),TC2区域的热惯性比较高, TC1区域的热惯性较低。注:用来测试曲线的回流炉温度稳定。
温度和PCB曲线
从物理学上讲,回流炉内温度与PCB之间存在以下关系:
· #1: 如果炉温高于PCB上的温度,那PCB温度就会升高。如果炉温低于PCB温度,那PCB温度就会降低。如果2者温度相同,那PCB温度就不变。
· #2:炉温和PCB温度相差越大,PCB温度变化率就会越大。
轨道附近的温度才真正影响曲线,温度曲线与回流炉设定温度有关,当然也与炉膛中的热空气回流相关。
图4显示了PCB上单独一个点的曲线。 每个区的设定温度都有标出来。温区的温度并不代表曲线的温度,从50度到70度的地方,PCB曲线已违反了第一条规则。即使在180度时,PCB的温度从160度降到了155度,按照第一条规则那PCB的温度应该一直上升的。
图5和图4类似,增加了一些梯形图.每一个台阶都是放置在炉内的热电偶的实际温度,这样看起来的话,PCB曲线是符合之前的2条规则的。
时间和PCB温度曲线
PCB在回流炉中停留的时间由链速快慢决定,链速越慢,PCB曲线就和回流炉的真实曲线接近。
事实上,的确是有很多回流炉的链速设定地非常慢,例如电子行业的厚膜电阻器以及烧结型银浆芯片贴装。 (见图 6).
加热效率及温度曲线
加热效率是指热量在多短的时间内可以传到PCB上,加热效率越高,回流炉不需要提高太多温度就可以让PCB在短时间内达到温度目标。
由于PCB尺寸和复杂程度的增加,元器件的密度分布更加不均匀,加热效率低的回流炉开始遇到一些问题。
这些回流炉使吸热量大的区域充分回流,导致吸热量小的区域过热了。不少新设计的回流炉有了更有效的加热系统以及更高的加热效率。
理想的PCB温度曲线
理想的PCB曲线通常包含三个因素:峰值温度,最大斜率,回流时间。
图7显示了一个典型的PCB曲线的温度分布。在下图中,峰值显示了每个测试点的的最高温度;最大斜率表示每秒钟时温度的最大变化;183以上温度表示了每个点在183度以上停留的时间。下图显示了每个测温点的目标值,这些值取自15家美国公司生产的产品。
最高温度
有铅焊锡的熔点在179°C – 183°C, 允许的最高温度上限为220°C 到 230°C,下限为195°C 到205°C.如果温度超过230度,会导致一些SMT零件损坏。 但如果温度不够,那么锡膏焊接就会出问题。
最大斜率
最大斜率指的是每秒钟的最大温度变化,也是指PCB每秒钟允许的最大温度变化,一些零件如果温度上升过快会导致开裂。零件能承受的最大温度变化率就是最大斜率。为了达到最大生产效率, PCB曲线的斜率一般低于最大允许值。对于大多数公司, 理想的上升斜率为1.0°C 到3.0°C/second. 对于气相焊, 预热区会使PCB温度以1-3 C/S上升到 70-80°C, 当到达气相区时上升斜率会达到 5.0°C/sec.
不解的是,下降斜率往往被忽视。一般来说,零件允许的最大斜率在上升和下降阶段是一致的,然而大多数公司关注的还是上升斜率部分。
在波峰炉上特别明显,波峰炉只有很短的冷却区, PCB很快从最高温度中回到正常温度。
回流时间
它用来衡量的PCB上锡膏的液化时间。大多数公司希望回流时间在30秒到60秒之间,然而一些吸热量很大的PCB往往需要90~120秒。如果锡膏的回流温度太长,锡铜金属化合物的过度增加会导致焊点过脆。
目前还不清楚为什么建议的最小回流时间是30秒。专家说焊接时间越短越好。可能只有3-6个热电偶贴在PCB上,那PCB上温度最低的点也许没有被测试到。还有一种可能,回流焊炉在生产过程中温度发生变化。那这个回流时间就不够了。
产品的温度曲线
许多产品的温度曲线不符合设定的目标值(峰值温度,最大斜率,回流时间)。在大多数情况下可以通过调整回流炉来满足任意两个在目标值,但是让三个目标值都符合要求就比较困难。如果增加了峰值温度,那回流时间可能超过范围,或者回流炉的预热区温度提高,最大斜率可能就超出范围了。
常用测温设备
最初的测温仪是一个条状图表记录器,用钓鱼线的方式让热电偶跟随PCB一起过炉,这样数据可以实时传回来,温度曲线打印在标准纸上。这种测温仪打印出的数据很难进行分析。不久回流炉制造商开始提供新的分析系统,可以把多达三根热电偶的曲线显示到计算机上。这些系统的优点是可以在电脑上进行数据的处理和分析。
因为钓鱼式测温存在的问题,新的便携式测温仪器出现了,它用电池供电、可以耐高温,一般有3-6个测试通道,出炉后可以通过RS232接口下载数据到电脑,显示出曲线画面。
尽管比前两种方法有了很大进步,但数据延时成了便携式测温仪的缺点。因为数据不是实时的传送回来,及时测温仪超温了也没办法知道。如果回流炉温度太高、传送带速度太慢、或者测温仪卡在炉膛内,那么PCB和测温仪都可能会损坏而无法修复。更换测温仪的成本相当高,而且在高温下测温仪必须使用隔热材料保温才行。为了改进这些缺点,新的测温系统被开发出来. 该系统把6根热电偶包在一根探管内,探管放在炉膛内部,连接到独立电脑上的采集卡,这样温度就可以实时的采集到了,并且探管可以承受高达450°C的高温。
便携式无线发射器
在1992年无线发射器出现了,可以提供实时的温度数据传输。这种发射器可以通过无线电发送6根热电偶的数据到接收器上,接收器连接到用户的电脑上收集温度,避免了繁琐的下载数据过程,该系统还具有一个额外的热电偶读数,可以连续发射器的内部温度以保证安全。
常用测温设备描述
大多数测温仪可以同时测试6根热电偶,可以在计算机上显示数据并打印出来,系统打印时可以用不同的颜色代表不同的热电偶。软件可以帮助分析峰值温度,最大斜率以及回流时间。图8是测温仪打印的曲线。
高级测温系统
在1989,我们为SMT行业设计出了更先进的温度分析系统,新系统不仅提供了常规分析还有附加功能。
除了有6个热电偶连接到PCB,系统在炉膛内内置了30个热电偶,每个探管包含了15个均匀间隔的热电偶。2组探管热电偶交叉排列,组合成30个均匀间隔的热电偶分布在炉子的加热区(见图9)。
30个热电偶在计算机屏幕显示出阶梯图,并且每五秒更新一次。图表显示沿回流炉内轨道处的实际温度(回流炉曲线)。图10显示了该系统的一个画面,可以实时监测炉温并且还另外有2个功能:预测曲线和24小时制程监控。
测试步骤
一般测温仪 vs.高级测温系统
一般测温仪 | 高级测温系统 |
使用测温仪测试炉温包含以下步骤: | 使用高级测温系统测试炉温包含以下步骤: |
1. 在PCB上粘贴热电偶. | 1. 在PCB上粘贴热电偶. |
2. 预设一个炉温和链速. | 2. 预设一个炉温和链速. |
3. 等待回流炉温度稳定 (often some uncertainty here)*. | 3. 等待回流炉温度稳定(the advanced profiler removes uncertainty)*. |
4. 用PCB过炉. | 4. 用PCB过炉. |
5. 分析数据 | 5. 分析数据 |
6. 重复步骤2-5,直到曲线符合要求 | 6. 在电脑上调整温度和链速直到曲线合格 |
7. 重复步骤2-6,直到曲线符合要求 | |
在测温过程中,重复每个步骤大约需要15-30分钟。可能需要重复2-10次,这需要看操作员的技能以及产品的复杂度。 | 测温过程中, 重复每个步骤大约需要15-30分钟。不过只需要重复2-3次即可, 操作员的技能以及产品的复杂度可以忽略。 |
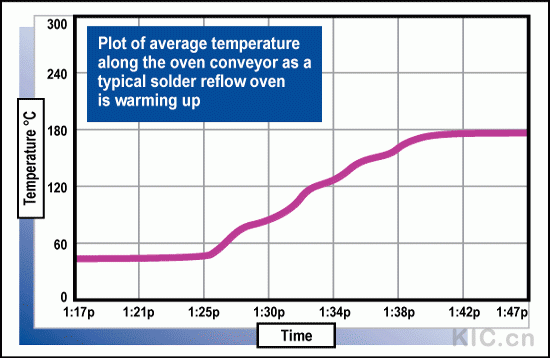
曲线预测
正如物理学的两个规律,PCB的温度和炉温直接相关。新的曲线测试系统融合了精确的算法,把回流炉温度和链速与PCB曲线联系起来,也就是曲线预测,允许用户在电脑上通过改变温度或链速进行实时预测。传统的测温仪需要15-20分钟才能测试出的结果,新曲线测试系统只需要几秒钟即可。
制程监测
新的曲线测试系统是一个完整的热工艺管理系统,它可以24小时不间断地监测回流炉制程。当回流炉稳定之后,该系统可以精确地显示出PCB对炉温的影响。它还能监测到生产过程中的炉温漂移,并触发声音报警。新系统的一个关键特点就是它可以重播炉温变化的过程,相当安装了一台曲线摄影机。
应当指出的是,现在一些测温仪也提供了预测曲线的功能,这些设备不能实时监测炉温,对于曲线测试系统它们有两个主要的缺点:
1. 传统的测温仪不能监测到回流炉的稳定性,用户只能通过回流炉的控制器来确定是否稳定。如果回流炉的温度在生产时发生改变,那温度曲线就不一样了。这种不稳定性,只有能独立监测炉内温度的系统才能探测到。
2. 如图4、5所示,设定的炉温不代表真实的炉温,如果传统的测温仪还靠这种关系来进行预测,那就没有精度可言了。
时间,精力和炉温猜测,这些都可以减少,必须要了解3个基本的要点:回流炉温度是不断变化的、曲线的基本原理和测试过程、曲线分析系统的类型。将这些知识将作为基本要点,可以减少操作时间;提高PCB产量;减少产品缺陷。